1. Production
Capacity: 1431ton/ year
Transparent glass cement: 731ton/year, 350g/pc, 2,088,571pcs
Black glass cement: 700ton/year, 500g/pc, 1,400,000pcs.
It can be customized according to your requirement.
2. Working time
16 hours/day, 300 days/year
3. Workers (It is only for your reference.)
Total workers: 10
5 workers for making glass cement
5 workers for sub-package of glass cement
4. Flow charts
4.1 Transparent glass cement
4.1.1 Drying for white carbon black by electrical heating furnace.
4.1.2 Making white carbon black small by three-roll grinder.
4.1.3 Dispersing and mixing for 107 adhesive 60%, white carbon black (sediment) 6%, white carbon black (gas doping) 2%, white oil 15%, silicone oil 15%, coupling reagent 2% by multifunction dispersion mixer, then trough hydraulic press machine to semi-automatic hard tube packing machine which filling the bottles.
4.1.4 Spraying the code on bottles by Ink-jet printing machine.
4.1.5 Put the finished products into the cartoons.
4.2 Black glass cement
4.2.1 Drying for white carbon black (gas doping) by electrical heating furnace.
4.2.2 Kneading 107 adhesive and calcium powder by vacuum kneader.
4.2.3 Making white carbon black and carbon black small by three-roll grinder.
4.2.4 Dispersing and mixing for 107 adhesive, white carbon black (gas doping) , white oil, silicone oil, coupling reagent, calcium powder, carbon black by multifunction dispersion mixer, then trough hydraulic press machine to semi-automatic hard tube packing machine which filling the bottles.
4.2.5 Spraying the code on bottles by Ink-jet printing machine.
4.2.6 Put the finished products into the cartoons.
5. Layout for the factory (reference only)
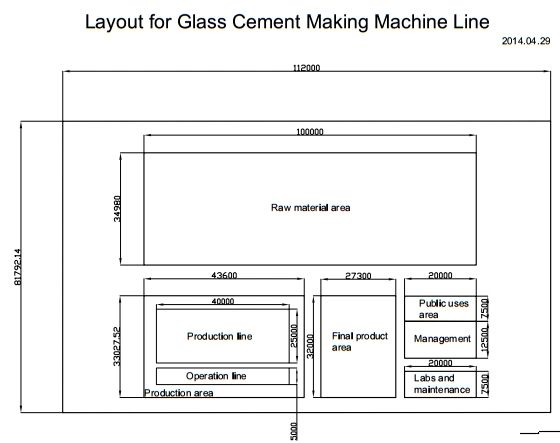
6. Finished Product Glass Cement
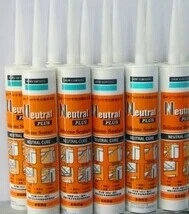
7. Machine List
Capacity: 1431ton/ year
Transparent glass cement: 731ton/year, 350g/pc, 2,088,571pcs
Black glass cement: 700ton/year, 500g/pc, 1,400,000pcs.
It can be customized according to your requirement.
2. Working time
16 hours/day, 300 days/year
3. Workers (It is only for your reference.)
Total workers: 10
5 workers for making glass cement
5 workers for sub-package of glass cement
4. Flow charts
4.1 Transparent glass cement
4.1.1 Drying for white carbon black by electrical heating furnace.
4.1.2 Making white carbon black small by three-roll grinder.
4.1.3 Dispersing and mixing for 107 adhesive 60%, white carbon black (sediment) 6%, white carbon black (gas doping) 2%, white oil 15%, silicone oil 15%, coupling reagent 2% by multifunction dispersion mixer, then trough hydraulic press machine to semi-automatic hard tube packing machine which filling the bottles.
4.1.4 Spraying the code on bottles by Ink-jet printing machine.
4.1.5 Put the finished products into the cartoons.
4.2 Black glass cement
4.2.1 Drying for white carbon black (gas doping) by electrical heating furnace.
4.2.2 Kneading 107 adhesive and calcium powder by vacuum kneader.
4.2.3 Making white carbon black and carbon black small by three-roll grinder.
4.2.4 Dispersing and mixing for 107 adhesive, white carbon black (gas doping) , white oil, silicone oil, coupling reagent, calcium powder, carbon black by multifunction dispersion mixer, then trough hydraulic press machine to semi-automatic hard tube packing machine which filling the bottles.
4.2.5 Spraying the code on bottles by Ink-jet printing machine.
4.2.6 Put the finished products into the cartoons.
5. Layout for the factory (reference only)
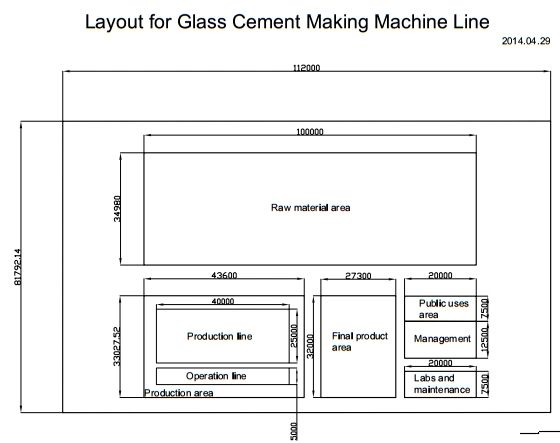
6. Finished Product Glass Cement
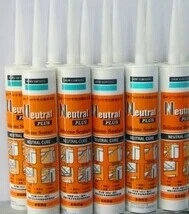
7. Machine List
Machine List |
Electrical heating furnace |
Vacuum kneader |
Three-roll grinder |
Multifunction dispersion mixer |
Hydraulic press machine |
Semi-automatic hard tube packing machine |
Ink-jet printing machine + Transfer belts |